t
The economical alternative
Laser Cladding instead of HVOF
up to 50% cost advantage!
Laser Cladding: the economical alternative to thermal spraying / HVOF
HVOF (High Velocity Oxygen Fuel) is a thermal spray process that has proven itself in the production of high-quality functional coatings. However, it is associated with high costs, which is why alternative processes are increasingly being used. Laser cladding is a superior alternative because it offers decisive advantages.
Advantages of laser cladding compared to HVOF
Laser cladding offers unbeatable advantages over thermal spray processes, especially HVOF:
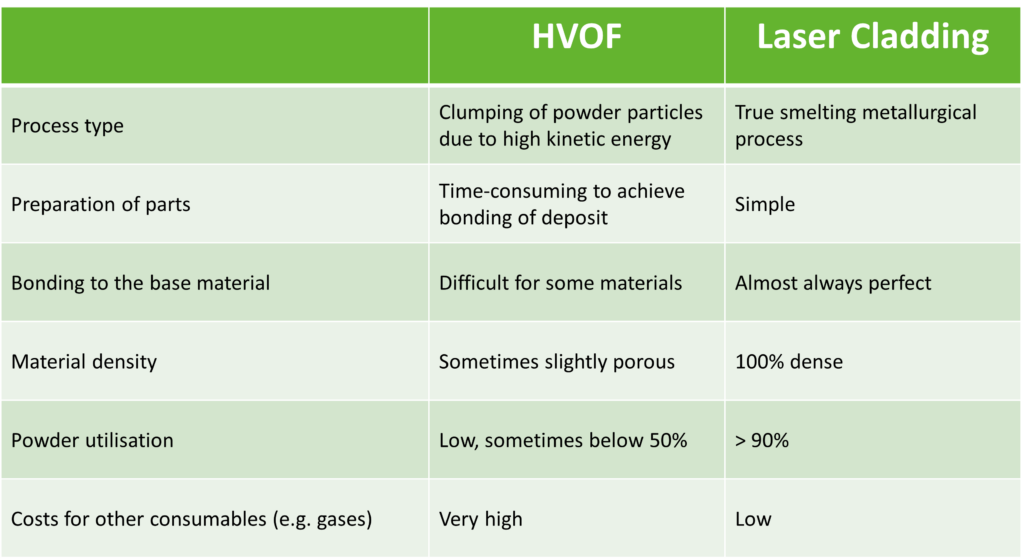
These advantages mean that coatings produced using laser cladding are up to 50% cheaper than comparable coatings produced using HVOF.
Other laser cladding/laser cladding/DED applications
Coating
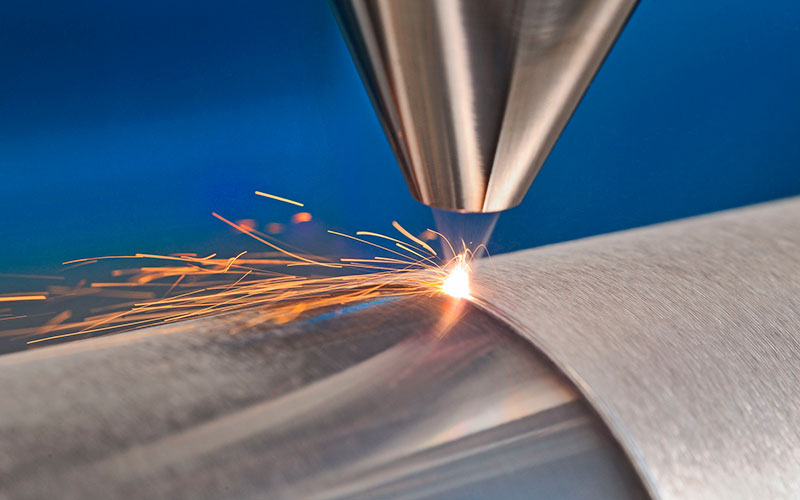
- Substitution hard chromium plating
- Substitution thermal spray
- Substitution conventional laser deposition
- So far uncoated components
Additives Manufacturing
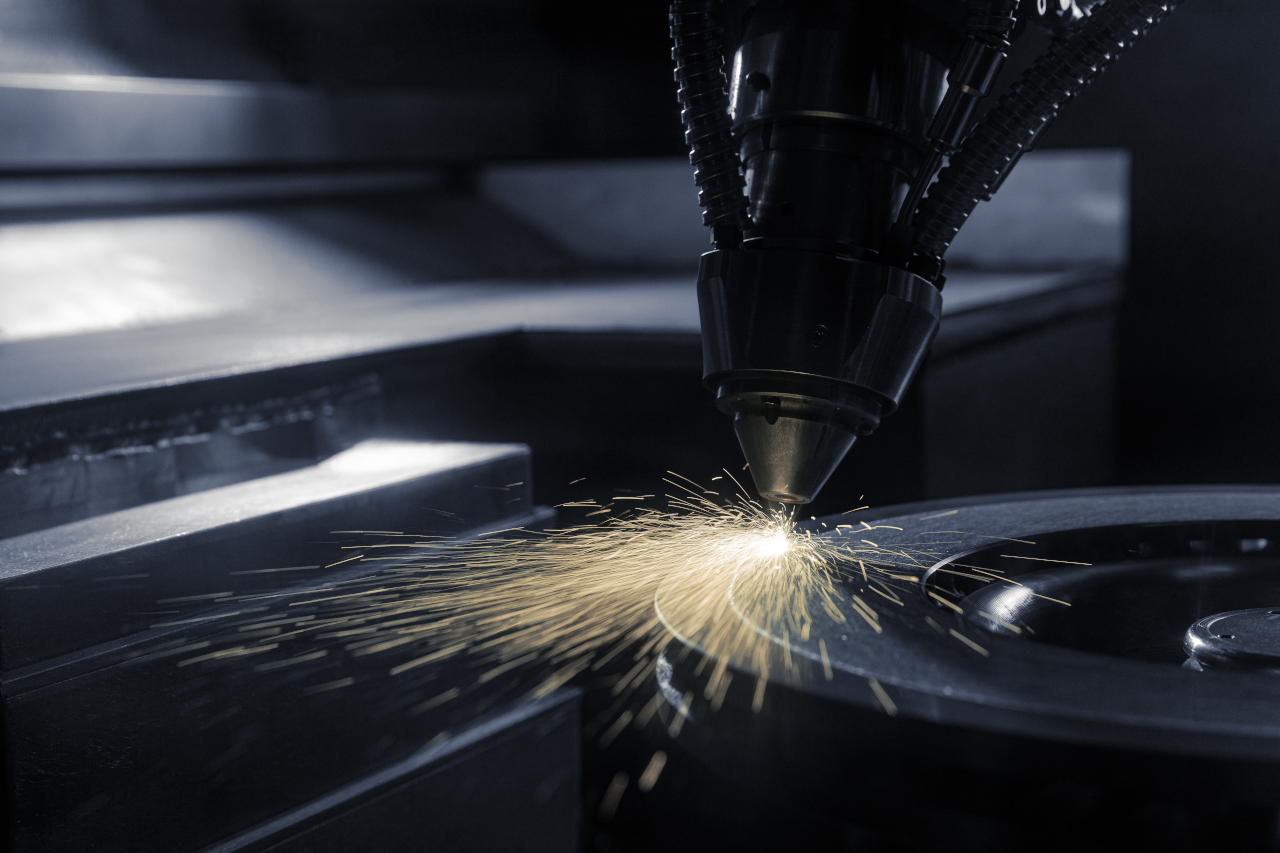
- Highly flexible production of geometric elements on semi-finished products, e.g. sealing lips or flanges (hybrid additive production)
- Functional integration
- In-situ combination processes (e.g. turning & AM)
Repair

- Repair of components that could not be repaired up to now due to the high heat input
- Mobile repair systems for conventional machine tools
Examples of possible materials
Matrix materials and corrosion protection
- Nickel alloys: NiCr, NiCrMo, NiCrBSi, …
- Iron alloys: 304L, 316L, 430L, 17-4-Ph, M2, …
- Cobalt alloys: CoCr, CoCrMo, CoCrW, CoCrW, …
- Others: titanium-, aluminium-, copper-, …
Hard phases/carbides
- Tungsten carbide
- Titanium carbide
- Chromium carbide
- Silicon carbide
- Molybdenum carbide
- …
Material content up to 60% by volume depending on combination
Contact us!
Your contact person for applications:
Dr.-Ing. Phillip Utsch
+49 241 6083 230
t