WECOGUARD
Quality assurance in laser cladding
Quality monitoring for laser cladding: WECOGUARD
Experience multidimensional real-time quality monitoring, efficient production transparency and comprehensive traceability in one place:
With WECOGUARD, you can manage quality deviations in real time and ensure that quality-relevant data is easy to understand and trace, even at a later date. WECOGUARD is a versatile system with advanced process sensors and product-neutral, AI-supported software developed to record critical coating parameters. An outstanding feature: the software combines the feed drive with quality-relevant process data, stores it in an AI-enabled database and assigns it to the produced component - making quality management easy!
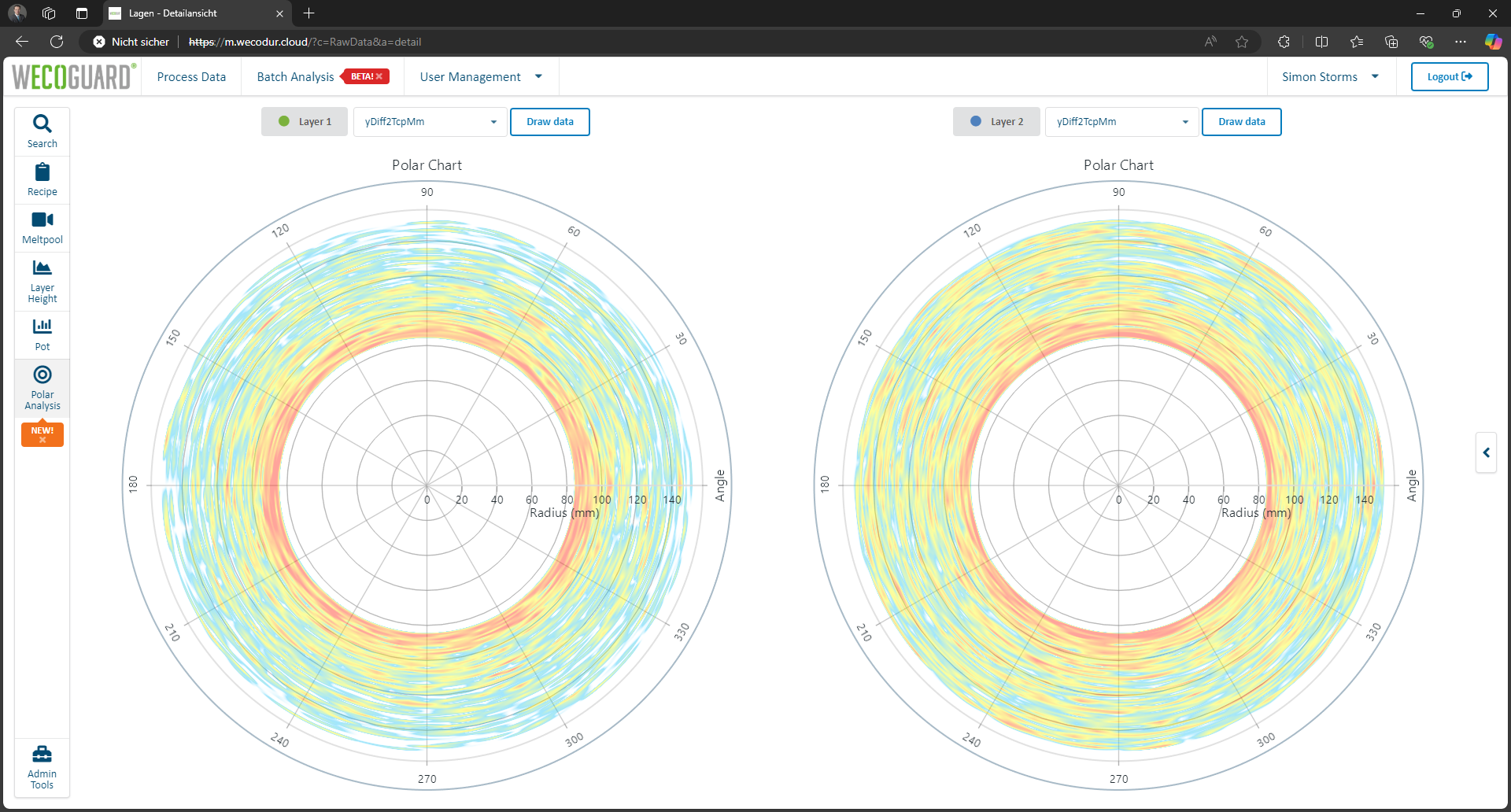
Monitoring in the lasercladding of brake disks
Imagine if you could check the quality of the coating by simply peeling it off, or - watch out - cutting an entire production line in half for metallographic analysis. Spoiler alert: Neither option is feasible.
But what if we told you that you don't have to?
Instead of slicing and dicing, WECOGUARD analyzes process data to detect coating defects before they become costly secrets. The nearly 4.5 billion sensor readings currently collected from high-speed laser coating processes reveal the hidden history of your coatings!
Deviating coating quality is a direct result of deviating process parameters, which are monitored and stored by WECOGUARD. This reveals the secret and enables targeted troubleshooting, as in the following example: a defective powder hose.
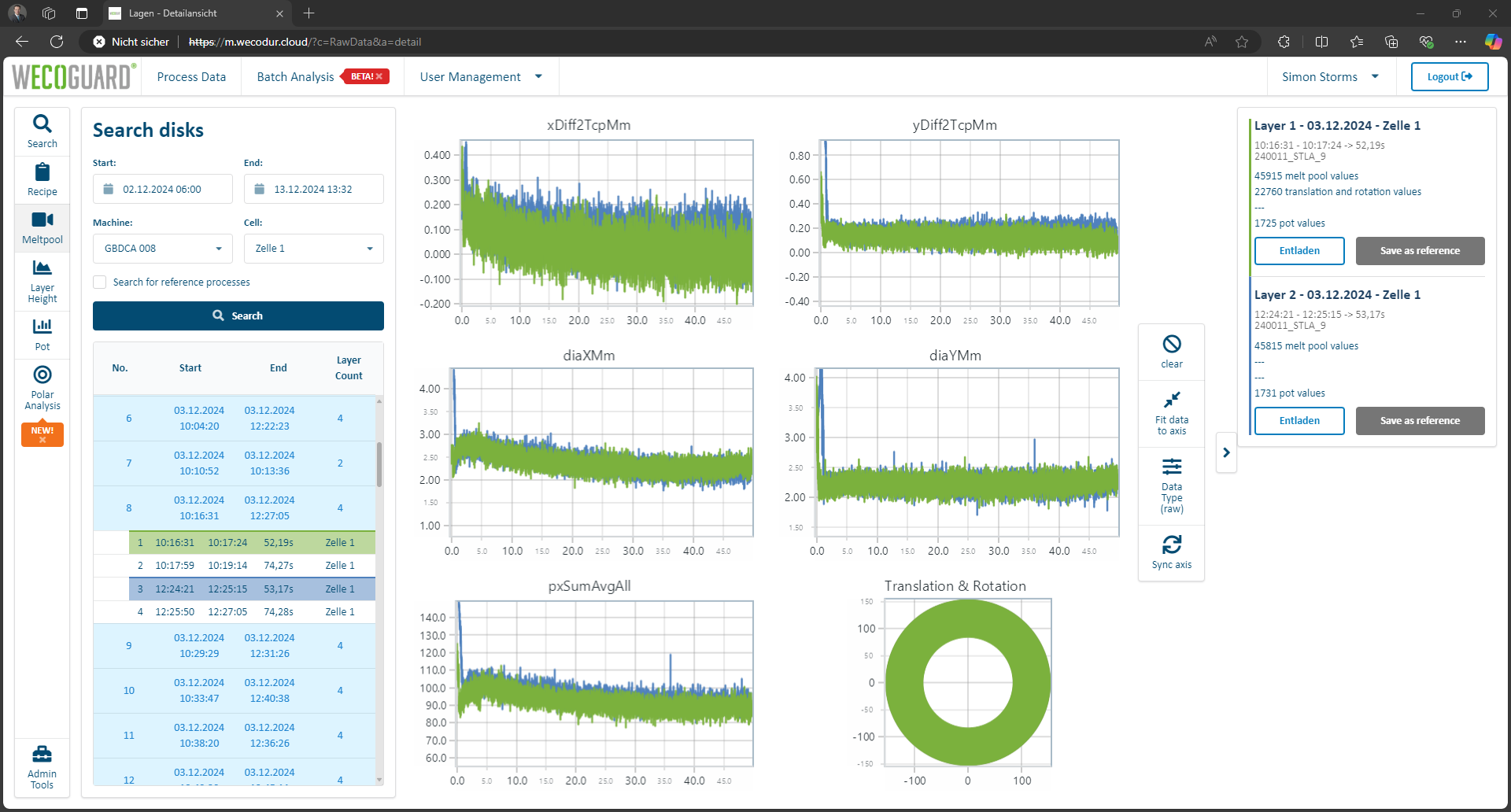
Quality assurance in series production for laser coating
In order to guarantee the quality of the coating, process-specific sensitive parameters must be identified and optimum process windows defined to take the guesswork out of quality control. So the big question is:
At what point does a deviation in certain parameters lead to coating defects, and how large does the deviation have to be for the result to be considered out of order?
The figure below shows the results of a sensitivity analysis conducted at HPL, where we used the WECOGUARD system to accurately track the process effects. As we deliberately varied the working distance, WECOGUARD monitored noticeable deviations in real time. Metallographic analysis confirmed these results, showing clear quality issues in the affected layers and confirming the correlation between parameter adjustments and coating performance.
This precise feedback loop transforms trial and error into actionable insights to efficiently define optimal process windows for reliable coating results.

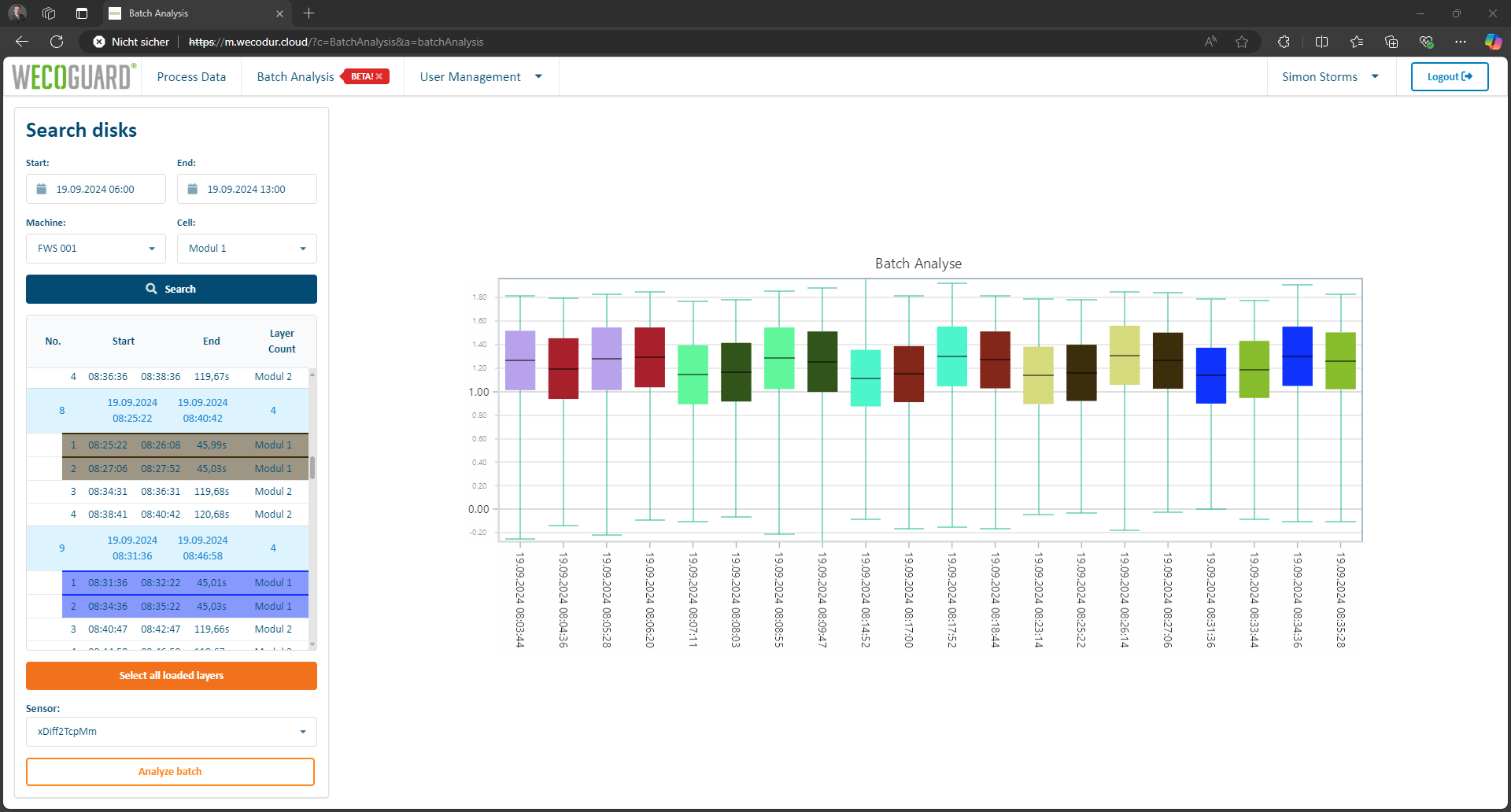