t
Future proof technology
High Speed Laser Cladding
for Hydraulic Components
The alternative to hard chrome plating: laser coating of hydraulic cylinders
Until now, hydraulic components have mostly been hard chrome-plated. However, the use of chromium VI-based processes is increasingly being discontinued due to legal regulations, as the associated risks to health and the environment are no longer acceptable. HPL laser cladding technology is an excellent alternative. It not only offers a more sustainable solution, but also usually significantly improved coating properties.
Make use of the advantages of high speed laser cladding for hydraulic components
HPL Technologies uses the high-speed laser cladding process in its machines and processes for coating hydraulic components. This process offers exceptionally high coating speeds and at the same time has a very low heat input into the base material. Another decisive advantage is the uniform layers with precise layer thickness - this reduces the normally very cost-intensive post-processing of the very hard layers to a minimum.
Other laser cladding/laser cladding/DED applications
Coating
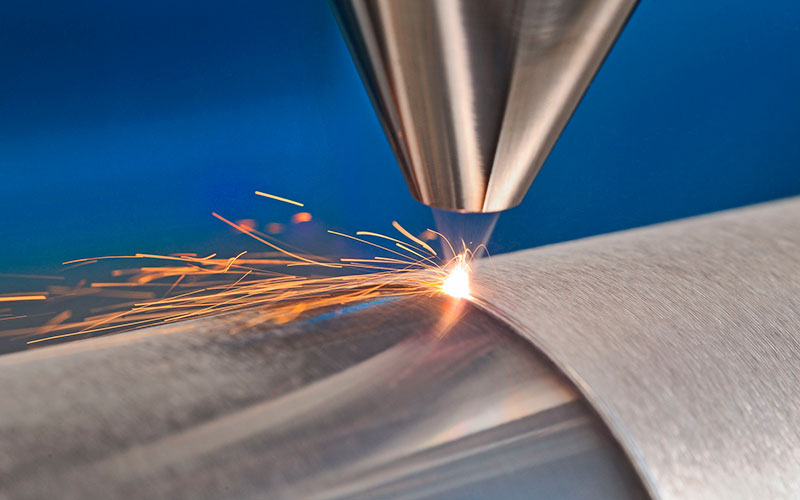
- Substitution hard chromium plating
- Substitution thermal spray
- Substitution conventional laser deposition
- So far uncoated components
Additives Manufacturing
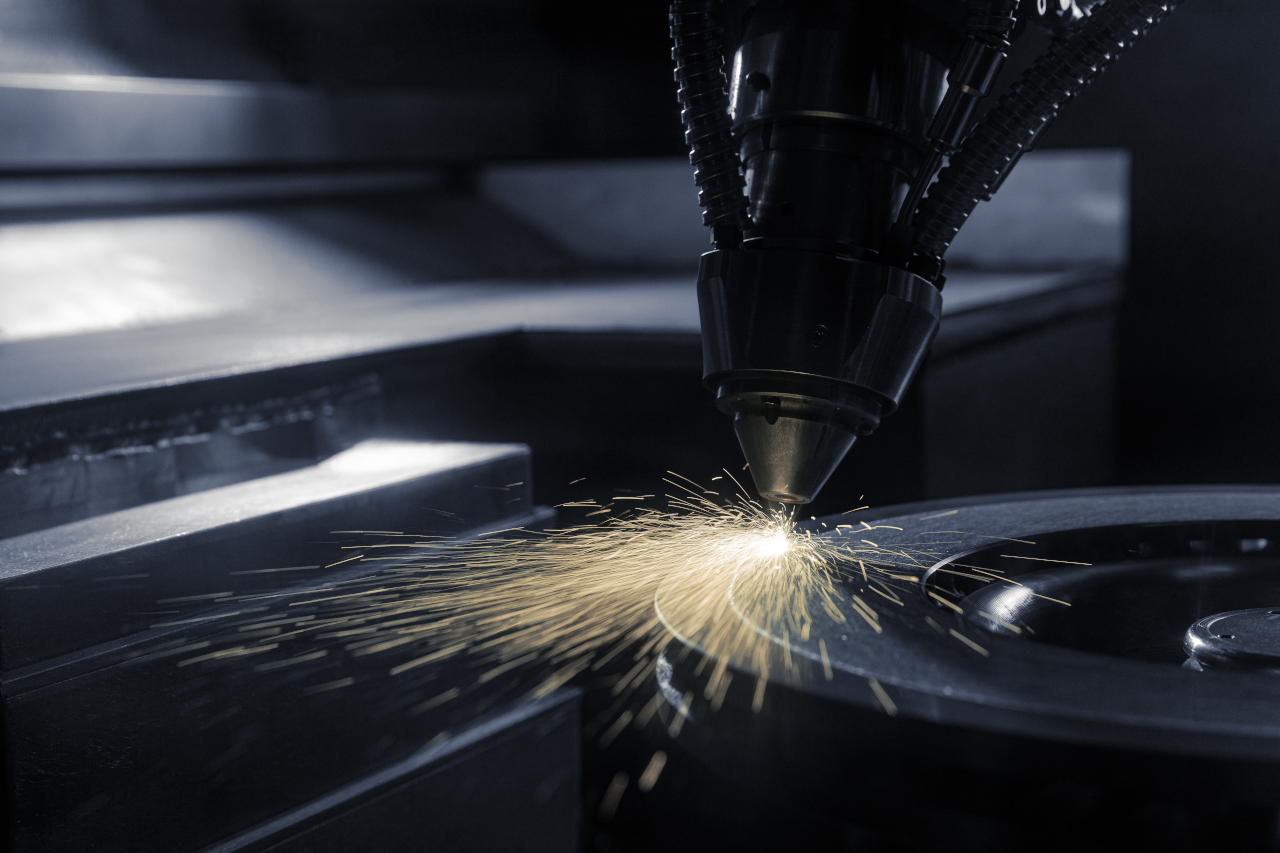
- Highly flexible production of geometric elements on semi-finished products, e.g. sealing lips or flanges (hybrid additive production)
- Functional integration
- In-situ combination processes (e.g. turning & AM)
Repair

- Repair of components that could not be repaired up to now due to the high heat input
- Mobile repair systems for conventional machine tools
Examples of possible materials
Matrix materials and corrosion protection
- Nickel alloys: NiCr, NiCrMo, NiCrBSi, …
- Iron alloys: 304L, 316L, 430L, 17-4-Ph, M2, …
- Cobalt alloys: CoCr, CoCrMo, CoCrW, CoCrW, …
- Others: titanium-, aluminium-, copper-, …
Hard phases/carbides
- Tungsten carbide
- Titanium carbide
- Chromium carbide
- Silicon carbide
- Molybdenum carbide
- …
Material content up to 60% by volume depending on combination
Contact us!
Your contact person for applications:
Dr.-Ing. Phillip Utsch
t