t
Economical and reliable
Laser Cladding Solutions: Rollers
for the Printing and Paper Industry
Surface engineering for printing rollers with laser coating
The paper and printing industry requires a wide variety of rollers. Depending on the application, different surfaces are required, which until now have often been applied by hard chrome plating or thermal spraying. Due to the requirement to replace chrome VI-based processes and the desire to use more efficient coatings, laser cladding is increasingly used. HPL laser technology enables a wide range of materials to be applied to rollers in the highest quality; for example nickel or cobalt-based alloys or iron-based alloys, which are chosen instead of chrome plating.
However, plain bearing layers produced using laser cladding can also be used in other industries. For example, they can be found in marine or automotive applications. Different materials are used, such as bronze alloys or white metal.
Advantages of high speed laser cladding for rollers
HPL laser coating solutions for the printing and paper industry are usually based on the high-speed laser cladding process. In this process, thin layers of the desired materials are applied very uniformly at very high coating rates. The advantages of the process are impressive: perfect coating quality, low thermal stress and therefore low distortion of the roller and significantly reduced post-processing costs.
Other laser cladding/laser cladding/DED applications
Coating
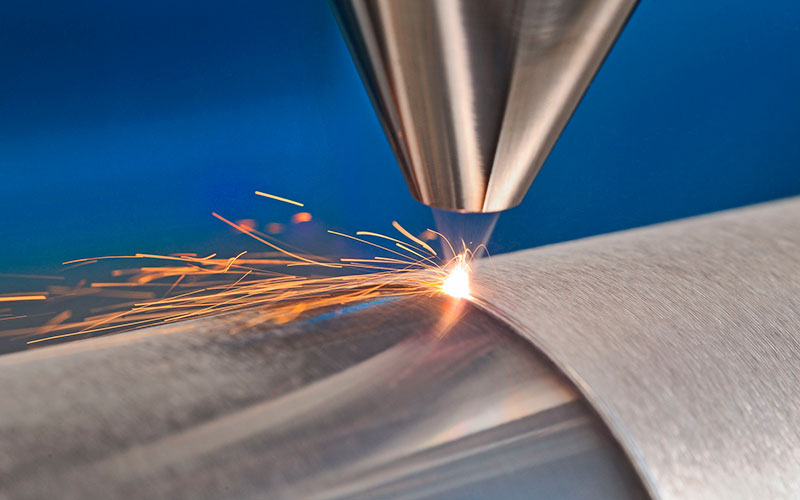
- Substitution hard chromium plating
- Substitution thermal spray
- Substitution conventional laser deposition
- So far uncoated components
Additives Manufacturing
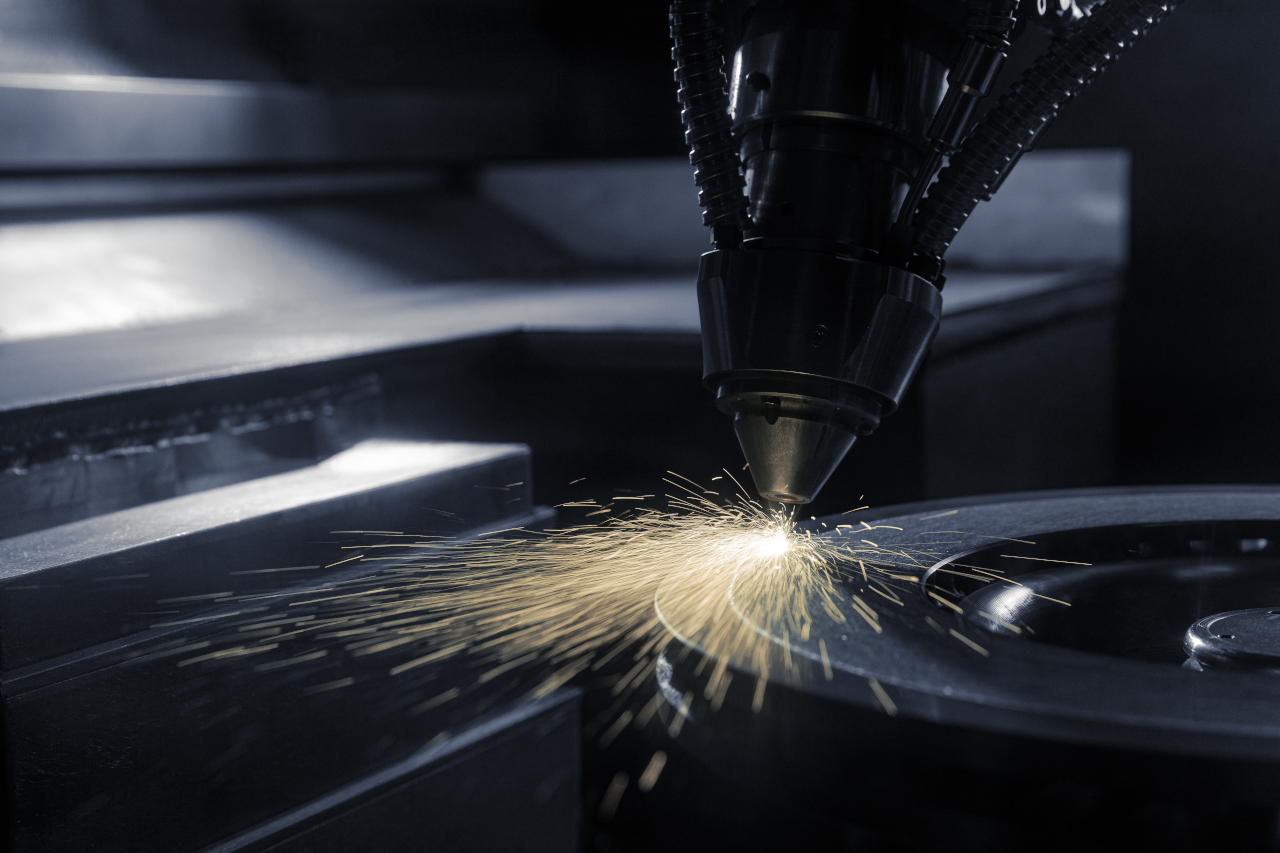
- Highly flexible production of geometric elements on semi-finished products, e.g. sealing lips or flanges (hybrid additive production)
- Functional integration
- In-situ combination processes (e.g. turning & AM)
Repair

- Repair of components that could not be repaired up to now due to the high heat input
- Mobile repair systems for conventional machine tools
Examples of possible materials
Matrix materials and corrosion protection
- Nickel alloys: NiCr, NiCrMo, NiCrBSi, …
- Iron alloys: 304L, 316L, 430L, 17-4-Ph, M2, …
- Cobalt alloys: CoCr, CoCrMo, CoCrW, CoCrW, …
- Others: titanium-, aluminium-, copper-, …
Hard phases/carbides
- Tungsten carbide
- Titanium carbide
- Chromium carbide
- Silicon carbide
- Molybdenum carbide
- …
Material content up to 60% by volume depending on combination
Contact us!
Your contact person for applications:
Dr.-Ing. Phillip Utsch
t